The Internet of Things (IoT) has emerged as a transformative technology with the potential to revolutionize various industries. Among these, the manufacturing sector stands out as a prime beneficiary of IoT advancements. By integrating IoT into manufacturing processes, businesses can achieve unprecedented levels of efficiency, productivity, and innovation. This blog explores the significance of IoT in the manufacturing industry, delving into its key applications, benefits, challenges, and future trends.
Understanding IoT and Industrial IoT
Let’s understand the basics first!
Definition and Basic Concept of IoT
The Internet of Things (IoT) refers to the network of interconnected devices that communicate and exchange data over the internet. These devices, embedded with sensors, software, and other technologies, collect and share data, enabling automation and smarter decision-making. IoT extends beyond consumer applications, playing a pivotal role in various industries, including healthcare, agriculture, and manufacturing.
Introduction to Industrial IoT (IIoT)
Industrial IoT (IIoT) specifically pertains to the application of IoT technologies in industrial environments. It involves the integration of sensors, instruments, and other devices within manufacturing systems to collect and analyze data. IIoT aims to optimize operations, enhance productivity, and improve overall industrial processes.
Differences between IoT and IIoT
While IoT encompasses a wide range of applications, IIoT is focused on industrial use cases. The primary distinction lies in the scale and criticality of operations. IIoT systems are designed to handle massive volumes of data and ensure reliability in harsh industrial environments. Additionally, IIoT emphasizes security, as any breach could disrupt essential manufacturing processes.
Importance of IIoT in Modern Manufacturing
The adoption of IIoT in manufacturing is driven by the need for increased efficiency, cost reduction, and improved product quality. By leveraging IIoT, manufacturers can gain real-time insights into their operations, enabling proactive maintenance, better resource management, and enhanced decision-making. IIoT is not just a technological upgrade; it is a strategic investment that can redefine competitive dynamics in the manufacturing industry.
Benefits of IoT in manufacturing
The IoT app boosts manufacturing. It helps to monitor and collect vital data for decision-making. IoT sensors and devices gather huge data from all levels of production. This helps manufacturers find issues that hinder the process flow. So, with the data flow, we can manage an output control loop. Automated systems can adjust production parameters in time. This leads to better resource use and less waste. For instance, a factory could have machines that manage energy use based on a room’s needs. This better management boosts efficiency and cuts wasted time. It enhances the manufacturing sector’s flexibility.
For this reason, IoT technologies are critical in manufacturing. They check and improve product quality. It lets them check essential factors, like temperature, pressure, and humidity, that may affect the products. Most of these sensors can detect tiny variances from the set parameters. They can then call for fixes before any defects occur. IoT-connected cameras and inspection systems can do online quality checks. They are more accurate than visual inspections. A focus on prevention and quality cuts substandard products in the market. It helps a company cut costs from rework, returns, and complaints.
IoT in manufacturing can save costs in many areas. There are many benefits. One is predictive maintenance using IoT sensors. They track equipment’s health and risk of failure. It enables planned maintenance. This cuts down on costly breakdowns and overhauls. Moreover, the IoT mechanism in tracking assets improves stock management and avoids the cost of overstocking or even outright stockout conditions. More efficient manufacturing processes produce less waste. This also cuts costs. IoT in customers’ analytics can help manufacturers. It can optimize production and reduce costs. This can boost profits and competitiveness.
Key Applications of IoT in Manufacturing
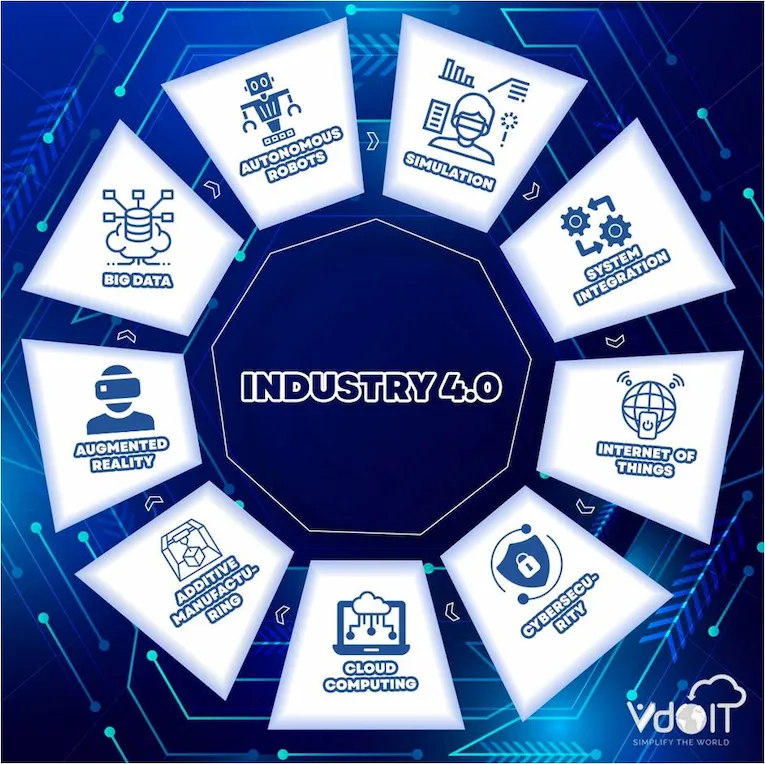
But where do we apply IoT in Manufacturing?
Smart Factories
A smart factory represents the epitome of IIoT implementation. These factories are equipped with interconnected devices and systems that communicate seamlessly to optimize production processes. IoT sensors monitor equipment performance, environmental conditions, and product quality in real-time.
This continuous flow of data allows for automated adjustments, reducing downtime and increasing efficiency. For instance, a smart factory can automatically adjust machine settings based on real-time data, ensuring optimal performance and minimizing waste.
Predictive Maintenance
Predictive maintenance is one of the most significant applications of IoT in manufacturing. Traditional maintenance schedules are based on fixed intervals, often leading to unnecessary downtime or unexpected equipment failures. IoT-enabled predictive maintenance uses sensor data to predict when a machine is likely to fail, allowing for timely intervention.
This approach not only reduces downtime but also extends the lifespan of machinery. For example, sensors on a production line can detect anomalies in vibration patterns, signaling the need for maintenance before a breakdown occurs.
Asset Tracking and Management
Effective asset tracking and management are crucial for efficient manufacturing operations. IoT solutions enable real-time tracking of assets, including raw materials, finished products, and equipment. This visibility ensures that inventory levels are optimized, reducing the risk of stockouts or overstocking.
Additionally, IoT-enabled tracking systems can streamline the supply chain, enhancing overall logistics and reducing costs. For instance, RFID tags and IoT sensors can provide real-time location data of materials, enabling just-in-time inventory management.
Quality Control
Maintaining high product quality is paramount in manufacturing. IoT technologies enhance quality control by providing real-time monitoring and data analytics. Sensors embedded in production equipment can detect defects or deviations from specifications, allowing for immediate corrective actions.
This proactive approach ensures that only products meeting quality standards reach the market. For example, IoT-enabled cameras can inspect products on the production line, identifying defects with greater accuracy than manual inspections.
Fun Fact : The number of Internet of Things (IoT) devices globally is expected to nearly double, from 15.9 billion in 2023 to more than 32.1 billion by 2030. In 2033, China will have the most IoT devices, with over 8 billion consumer gadgets. (Source: Statista)
Benefits of Implementing IoT in Manufacturing
Here are the main benefits of IOT in the manufacturing industry!
Improved Operational Efficiency
The integration of IoT in manufacturing leads to significant improvements in operational efficiency. Real-time data collection and analysis enable manufacturers to identify bottlenecks, optimize processes, and reduce waste.
Automated systems can adjust production parameters dynamically, ensuring that resources are used efficiently. For instance, IoT sensors can monitor energy consumption, allowing for adjustments that reduce energy costs without compromising production output.
Cost Reduction
Implementing IoT technologies can result in substantial cost savings for manufacturers. Predictive maintenance minimizes downtime and repair costs, while optimized asset management reduces inventory carrying costs.
Additionally, improved operational efficiency translates to lower production costs. For example, by using IoT data to fine-tune production processes, manufacturers can reduce material waste and enhance energy efficiency, leading to cost reductions.
Enhanced Product Quality
IoT enables continuous monitoring and real-time adjustments, ensuring that products meet high-quality standards. This capability not only enhances customer satisfaction but also reduces the costs associated with rework and returns.
For instance, IoT sensors can detect and address quality issues during production, preventing defective products from reaching customers and damaging the company’s reputation.
Better Decision Making through Data Analytics
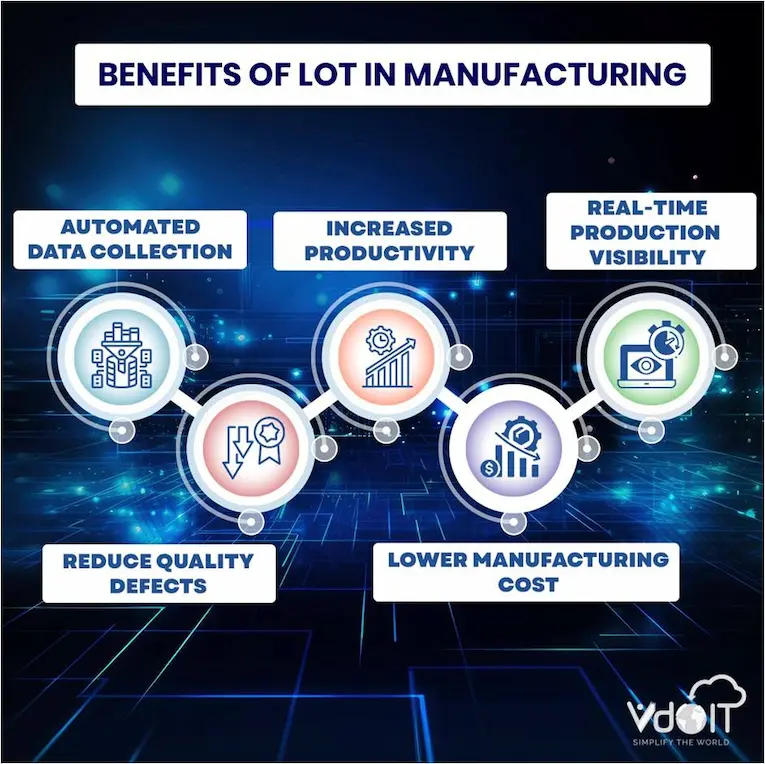
IoT generates vast amounts of data that, when analyzed, provide valuable insights into manufacturing operations. These insights support informed decision-making, from optimizing production schedules to enhancing supply chain management.
Data analytics can reveal trends and patterns that were previously hidden, enabling manufacturers to make strategic decisions based on real-time information. For example, data analytics can identify correlations between machine performance and product quality, guiding improvements in production processes.
Increased Flexibility and Scalability
IoT technologies provide manufacturers with the flexibility to adapt to changing market demands. IoT-enabled systems can be easily reconfigured to accommodate new products or production methods.
Moreover, the scalability of IoT solutions allows manufacturers to expand their operations without significant disruptions. For instance, IoT platforms can integrate new devices and sensors seamlessly, supporting the growth and diversification of manufacturing processes.
Challenges and Solutions in Implementing IoT
Let’s take a look at the main challenges to implementing IoT in manufacturing!
Data Security and Privacy Concerns
The widespread use of IoT devices in manufacturing raises significant data security and privacy concerns. Cyberattacks targeting IoT systems can disrupt operations and compromise sensitive data.
Manufacturers must implement robust security measures, such as encryption, authentication, and regular security audits, to protect their IoT infrastructure. For example, deploying firewalls and intrusion detection systems can safeguard IoT networks from unauthorized access.
Integration with Legacy Systems
Many manufacturing facilities rely on legacy systems that are not designed to integrate with modern IoT technologies. This incompatibility poses a challenge to seamless IoT implementation.
Manufacturers can address this issue by adopting middleware solutions that enable communication between legacy systems and IoT devices. Additionally, phased integration strategies can ensure a smooth transition without disrupting ongoing operations. For example, implementing IoT gradually in specific areas of the production line can help identify and resolve integration challenges.
High Initial Investment Costs
The initial investment required for IoT implementation can be substantial, encompassing costs for hardware, software, and infrastructure upgrades. However, the long-term benefits, including cost savings and efficiency gains, often justify the investment.
Manufacturers can explore financing options, such as leasing IoT equipment or partnering with IoT solution providers, to mitigate the financial burden. For instance, subscription-based models for IoT services can spread out costs over time, making implementation more affordable.
Need for Skilled Workforce
The successful deployment and management of IoT systems require a skilled workforce proficient in IoT technologies and data analytics. Manufacturers must invest in training and development programs to upskill their employees.
Collaborating with educational institutions and industry organizations can also help bridge the skills gap. For example, offering IoT certification programs and workshops can equip employees with the necessary skills to manage and optimize IoT systems effectively.
Solutions and Strategies to Overcome These Challenges
To overcome the challenges of IoT implementation, manufacturers should adopt a strategic approach that includes the following steps:
- Conducting a thorough assessment of current systems and identifying areas for IoT integration
- Developing a clear IoT implementation roadmap with defined goals and timelines
- Ensuring robust data security measures are in place to protect IoT infrastructure
- Investing in employee training programs to build a skilled workforce
- Exploring financing options and partnerships to manage initial investment costs
- By addressing these challenges proactively, manufacturers can unlock the full potential of IoT and drive transformative improvements in their operations.
Advancements in IoT Technology
The field of IoT is continuously evolving, with advancements that promise to further enhance its impact on manufacturing. Emerging technologies such as 5G, edge computing, and advanced sensors are set to revolutionize IIoT applications.
For instance, 5G connectivity will provide faster and more reliable communication between IoT devices, enabling real-time data processing and decision-making. Similarly, edge computing will allow data to be processed closer to the source, reducing latency and improving response times.
Emerging Applications of IoT in Manufacturing
As IoT technology advances, new applications are emerging that offer even greater benefits to manufacturers. These include:
- Autonomous mobile robots (AMRs) for material handling and logistics
- Augmented reality (AR) and virtual reality (VR) for training and remote maintenance
- Digital twins for real-time simulation and optimization of manufacturing processes
For example, digital twins can create virtual replicas of physical assets, allowing manufacturers to test and optimize production processes in a virtual environment before implementing changes on the shop floor.
The Role of AI and Machine Learning in Enhancing IIoT
Artificial intelligence (AI) and machine learning (ML) are playing an increasingly important role in enhancing IIoT applications. By analyzing vast amounts of data, AI and ML algorithms can identify patterns, predict outcomes, and optimize processes.
For instance, AI-driven predictive maintenance systems can not only predict equipment failures but also recommend optimal maintenance schedules and procedures. Similarly, ML algorithms can optimize production parameters in real-time, improving efficiency and product quality.
Predictions for the Future of IIoT in the Manufacturing Industry
The future of IIoT in the manufacturing industry is bright, with several key trends expected to shape its evolution:
- Increased adoption of IoT-enabled automation and robotics
- Greater focus on sustainability and energy efficiency through IoT solutions
- Expansion of IoT ecosystems with interconnected devices and systems
- Enhanced collaboration and data sharing across supply chains using IoT platforms
As these trends unfold, IIoT will continue to drive innovation, efficiency, and competitiveness in the manufacturing sector.
Embracing IoT for a Smarter Manufacturing Future
The integration of IoT in manufacturing is transforming the industry, offering unprecedented opportunities for efficiency, productivity, and innovation. From smart factories to predictive maintenance, IoT applications are revolutionizing manufacturing processes and delivering significant benefits.
However, the journey to full IoT implementation comes with challenges that require strategic planning and investment. By embracing IoT technologies and addressing these challenges, manufacturers can gain a competitive edge and pave the way for a smarter, more efficient future.
The transformative potential of IoT in manufacturing is undeniable. As IoT technology continues to advance, its impact on the industry will only grow, driving further improvements in operational efficiency, product quality, and overall competitiveness. Embracing IIoT is not just an option for manufacturers; it is a necessity for those who aim to thrive in the digital age.
Connect with the best IOT development company today to know more!
FAQ: iot in manufacturing
What does the Internet of Things (IoT) mean in manufacturing?
In manufacturing, IoT refers to connected objects that share data. It aims to improve production by providing real-time information across the assembly line.
What are the differences between IIoT and others?
IIoT is different from IoT. It targets industrial applications. It handles big data and must work reliably in harsh environments. It focuses on security and is more specific than IoT. IIoT is for critical manufacturing operations.
What is the advantage of deploying IoT in manufacturing?
IoT optimizes processes, cuts costs, and boosts product quality. It also enables reliable data analysis for business decisions and is flexible and adaptable to market trends.
Which key role does IoT play in predicting maintenance in manufacturing?
With the proposed bi-directional IoT, the regular or random failure of equipment can be predicted from the sensor data and maintenance intervention carried out on time. It saves time, makes equipment last longer, and cuts repair costs. Fixing problems when they are small prevents bigger issues.
What factors make IoT implementation challenging for manufacturers?
Major issues with IoT include data security and privacy. There are also concerns about integrating it with existing systems. Other issues include high initial costs and a lack of skilled IoT and data analysis experts.
What do people mean by, say, an intelligent factory, and how do they apply IoT?
A factory combining IoT devices and systems tracks and controls production precisely. This allows for pre-programming adjustments. They improve the machinery’s efficiency and productivity.
In what way, does IoT benefit product quality in manufacturing?
Through IoT technologies during production, it is possible to monitor the procedure or process incessantly and make changes when necessary. Sensors report defects or variations. They prompt immediate corrections in manufacturing. So, perfect products are released into the market.